Students at the University of California San Diego (USCD) have tested a liquid fueled, 3D printed rocket engine using a technique that has never been used to build a rocket before anywhere in the World aside from NASA.
The students have built and successfully test fired a rocket that uses kerosene and liquid oxygen for the $6,800 which was suggested and partly funded by NASA as part of the Marshall Space Flight Center. The test was devised to see whether or not 3D printed parts could actually be used for a rocket.
The injector used a fuel-oxidizer-oxidizer-fuel intel arrangement. The cooling jacket was able to keep heat compartmentalized so that the chamber walls were kept as cool as possible. The engine itself (DMLS). During this process, thin layers of chromium cobalt are repeatedly spread and fused to the component and the excess powder is removed. The final piece has all temporary supports removed before being hardened, then polished and built. The result is an extremely quick and cheap way to build rocket parts. By using 3D printing, build time for parts can be reduced from weeks to hours.
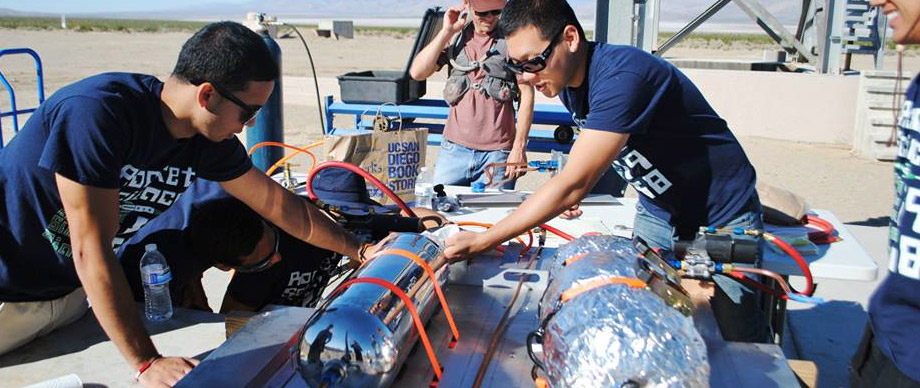
The fire test which took place during the Friends of Amateur Rocketry launch was designed to see if the engines could power the third stage of a Nanosat launcher. These are only required to launch smaller satellites weighing less than 1.33kg. As a result, the team came up with a rocket engine that is 7 inches (17.7cm) long with a weight of only 200lbs (90.7kg). NASA provided $5000 of the total build costs with students raising the remaining money by organizing various fundraising activities.
The rocket engine, labelled Tri-D has proven that printed engine parts can indeed be used. This could mean the speedier manufacture of rockets at a vastly reduced cost.
The students have built and successfully test fired a rocket that uses kerosene and liquid oxygen for the $6,800 which was suggested and partly funded by NASA as part of the Marshall Space Flight Center. The test was devised to see whether or not 3D printed parts could actually be used for a rocket.
The injector used a fuel-oxidizer-oxidizer-fuel intel arrangement. The cooling jacket was able to keep heat compartmentalized so that the chamber walls were kept as cool as possible. The engine itself (DMLS). During this process, thin layers of chromium cobalt are repeatedly spread and fused to the component and the excess powder is removed. The final piece has all temporary supports removed before being hardened, then polished and built. The result is an extremely quick and cheap way to build rocket parts. By using 3D printing, build time for parts can be reduced from weeks to hours.
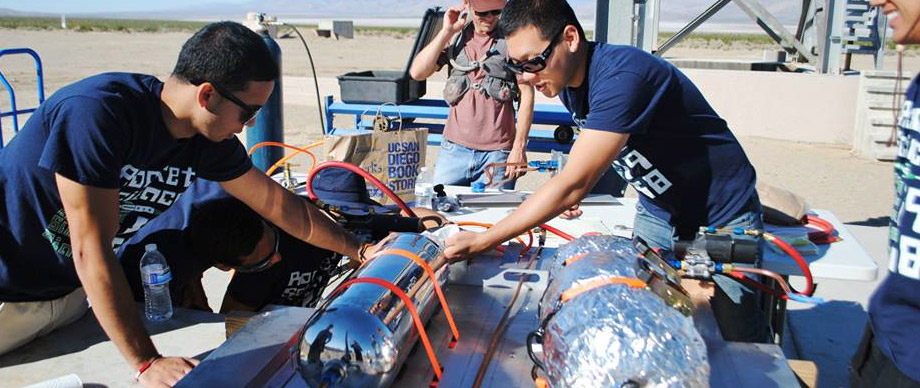
The fire test which took place during the Friends of Amateur Rocketry launch was designed to see if the engines could power the third stage of a Nanosat launcher. These are only required to launch smaller satellites weighing less than 1.33kg. As a result, the team came up with a rocket engine that is 7 inches (17.7cm) long with a weight of only 200lbs (90.7kg). NASA provided $5000 of the total build costs with students raising the remaining money by organizing various fundraising activities.
The rocket engine, labelled Tri-D has proven that printed engine parts can indeed be used. This could mean the speedier manufacture of rockets at a vastly reduced cost.
0 comments:
Post a Comment